Frequency converters increase the performance of electric motors and reduce energy consumption
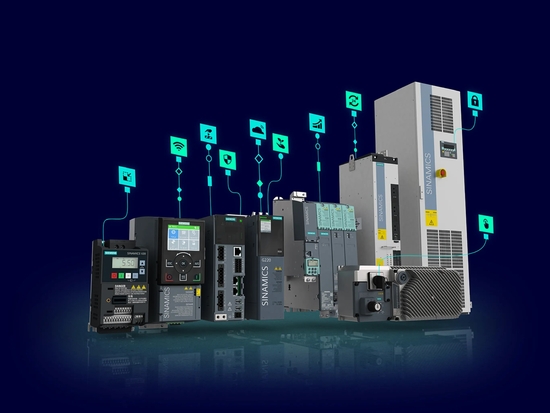
In every industry, electric motors are a key element. An equally important part of the drive units are the frequency converters, which provide the drives with flexibility, reliability and energy efficiency during operation.
Correct use of the frequency converter can significantly optimize performance and at the same time significantly reduce energy costs. Of course, assuming the correct application of both the electric motor and the frequency converter.
Electric motor speed regulation
A frequency converter is a device that converts direct current (DC) or alternating current (AC) into a current with a different frequency and voltage, thereby regulating the speed of the electric motor and enabling precise control of the speed and torque of the drive.
Due to their ability to control frequency and voltage, these converters are an essential element in many industrial processes, such as power units, welding and measuring equipment, temperature controllers, etc.
Tip: you can read more information about the operation of frequency converters in this article
Performance optimization
One of the key factors when using frequency converters is performance optimization. This includes configuring the drive correctly for the application, setting the frequency and voltage to match system requirements, and minimizing conversion power losses.
Modern devices, such as SINAMICS frequency converters, often provide the ability to adjust performance using sophisticated control algorithms. This feature allows the drive output to be dynamically adjusted in real-time to the needs of the application, maximizing efficiency and performance.
Energy saving
Another important aspect is the reduction of energy consumption, which is a key factor for 2 reasons. It can significantly reduce energy costs while contributing to environmental sustainability.
Frequency converters can reduce energy consumption in several ways:
Energy recovery – modern frequency converters often allow energy recovery from other processes, thus minimizing energy loss.
Variable frequency – setting the frequency of the inverter according to the current needs of the application can reduce energy consumption by limiting unnecessary losses in unused power.
Efficient control – intelligent control algorithms allow the inverter output to be optimized to minimize energy losses and maximize efficiency under various operating conditions.
Frequency converters have a wide range of applications
Frequency converters are widely used in industries such as manufacturing, transportation, energy, and many others. They are applied, for example, to drive motors during processing, machining, moving, pumping, ventilation, positioning, gas compression, temperature control, lighting, for various types of welding, etc.
Frequency converters are an integral part of modern industrial technology, and their effective use can significantly increase performance and energy savings. To achieve optimal results, it is crucial to select the right type of inverter for the application and to configure and maintain it professionally.
The combination of the correct selection of the converter, its professional implementation, setting and subsequent efficient operation can increase and improve the performance of the electric motor, while reducing energy costs.
TIP: in our configurator you will find a number of SINAMICS frequency converters divided according to the purpose of use.